Gunpowder mills
Nathanael Hodge
Summary
Gunpowder, made from saltpetre, charcoal and sulphur, originated in China in the 9th century and was known in the west from the 13th century. Originally made in small quantities in a pestle and mortar, water powered gunpowder mills became common the 16th century. The process of manufacture involved preparing the ingredients and mixing them in the right quantities before ‘incorporating’ them in a stamping mill, or later an edge runner mill. Further stages of the process included pressing, corning, granulating, glazing and drying, before the final result was packaged in wooden barrels. Gunpowder gradually fell out of use after newer explosives were developed in the 19th century.
Details
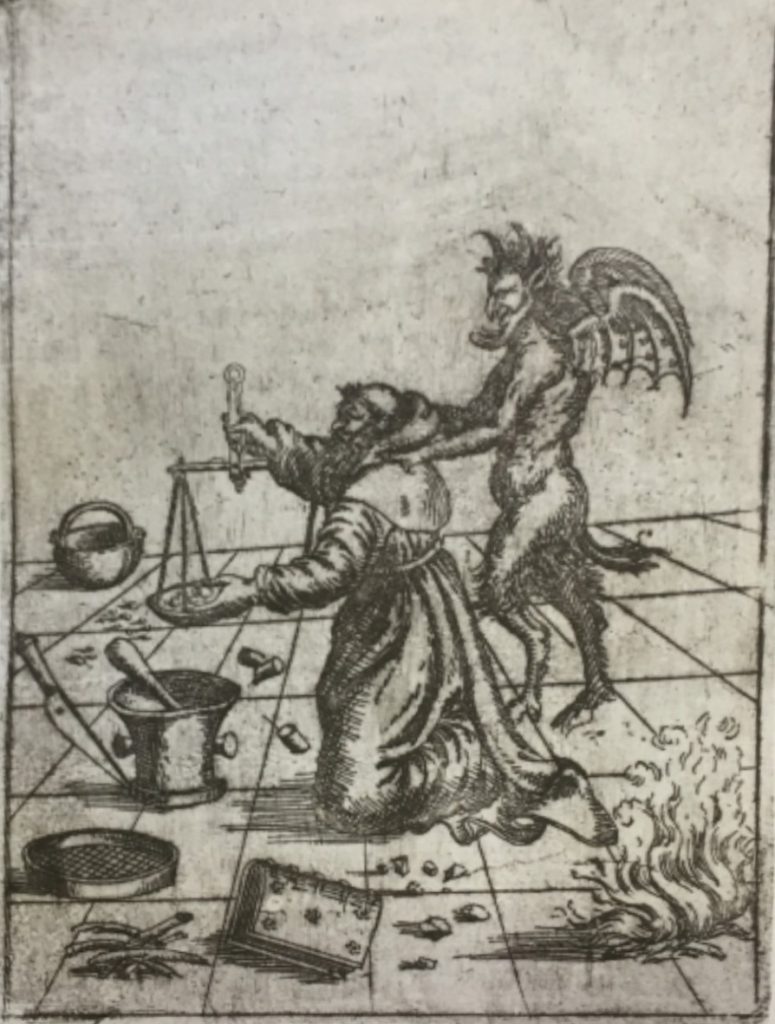
Although medieval Europeans gave the devil the credit for the invention of gunpowder, it was in fact Chinese alchemists who first began to manufacture it in the 9th century. It travelled through the Islamic World along the Silk Roads, and it is first mentioned in the West in the 13th century by Roger Bacon.
Gunpowder, or black powder, is a mixture of saltpetre, charcoal and sulphur. At first made in small amounts in a pestle and mortar, from the 16th century there were water driven mills in England, and from 1589 these had to have a royal licence to operate, although some operated illegally.
The first stage in the manufacture of black powder was the preparation of the ingredients. Saltpetre (potassium nitrate) could be manufactured from decomposed animal dung, mixed with lime. Sulphur was imported from Italy and Sicily, while charcoal was made by charring wood. Powder mills were often surrounded by coppices of willow and alder trees for this reason. Before being mixed together the ingredients had to be powdered and sieved and weighed to ensure the right quantities were used, the proportions being 75 parts saltpetre to 15 parts charcoal and 10 parts sulphur. They were then mixed together in a revolving drum to form ‘green charge’.
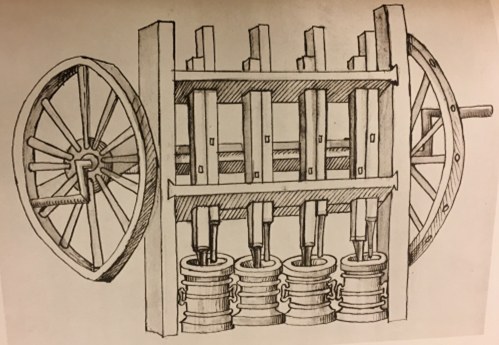
The next stage was incorporating. The earlier form of incorporating mill was the pestle or stamping mill, in which the turning camshaft caused stamps to rise and fall, beating the powder in troughs below. These could be powered by hand, by treadmill or by waterwheel. Later, edge runner stones became common, and the earlier stamping mills were made illegal in 1772 on safety grounds.
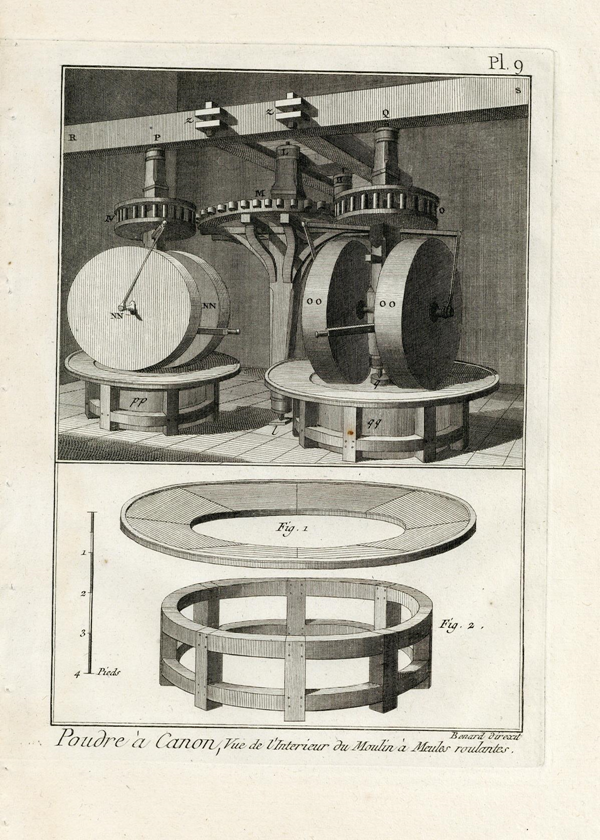
The charge needed to be kept damp throughout the incorporating process. The process as carried out at the Royal Gunpowder Factory at Faversham is described in a 1798 notebook in the Mills Archive’s collections:
Process of Making Gunpowder at Faversham
… The whole is placed in a Tub, having a Kind of Rack which is turned round to mix the Ingredients, it is then put into a Box or hopper … in which is a Machine for stiring it about, from that Box it is taken to the Mill Room and there passed thro another mixing Tub, 30 lb are then put under each pair of Stones with a little Water, which is also added from time to time as it works dry. 5 Hours are required at Faversham, and at Waltham Abby to work paste owing to the greater Body and height of Water at the latter place, and as the goodness of Powder is increased by the quickness of Working, Waltham Abby Powder exceeded that of Faversham as 190 to 169. The Mills work constantly Day and Night, the men are relieved every 6 hours …
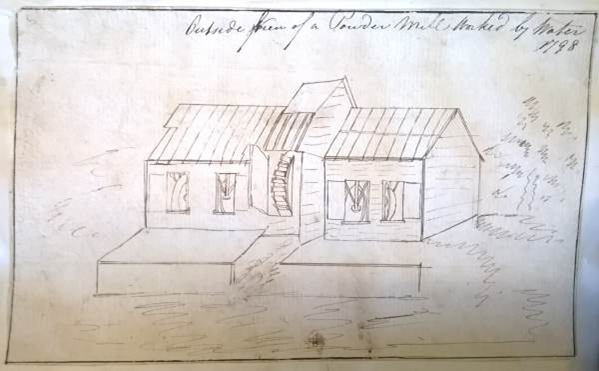
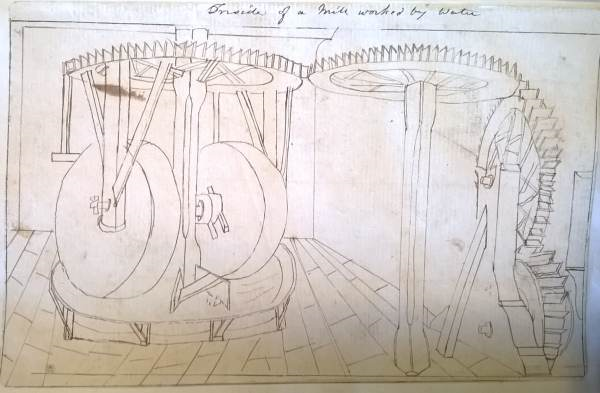
In the 19th century steam power was introduced, as well as water turbines.
Originally the incorporated powder was then dried and stored for use. However it did not explode consistently, and the ingredients would separate out again. To remedy this further stages were added to the manufacture process. The powder was pressed, and then placed in a corning machine, in which it was passed through parchment sieves. It was then granulated and glazed with black lead to make the grains resistant to moisture. Then it was dried in heated stoves, before being packaged in oak barrels. These were manufactured on site, and coopers made up a large part of the workforce of a powder mill.
Accidents were common, especially in the incorporating mill. At Waltham Abbey in 1861, for example, the workmen failed to put a piece of leather under the edge runner stones when moving them and this lead to a spark which ignited the powder. Four men were badly burnt, one of whom died.
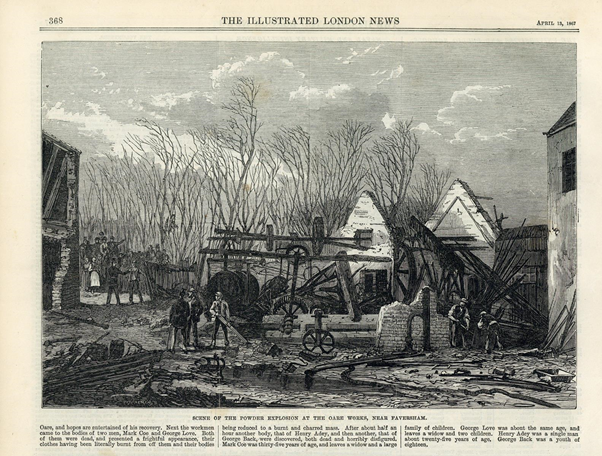
In the 19th century new varieties of powder were developed, alongside other new forms of explosive, such as Alfred Nobels’ dynamite. Existing gunpowder mills expanded to manufacture these new products. Black powder was still used for fuses, fireworks and blasting in slate quarries. By the late 20th century the last gunpowder factories in the UK had closed and black powder was only available by import.
Links
Crocker, Glenys, The Gunpowder Industry (Shire Publications, 1986)
More information about gunpowder mills can be found in these articles:
- Powder mills
- An explosive business
- Gems of the Archive: Milling with a bang!
- The Devil’s Art: The History of Gunpowder Manufacture
- Archivist’s Pick: Notes on gunpowder manufacture
Other images and documents in the archive catalogue.
List of gunpowder mills in our database.
From elsewhere on the web: Royal Gunpowder Mills, Waltham Abbey