Saw mills
Mildred Cookson
Summary
The main function of wind or water powered saw mills was to convert tree trunks, logs, into planks.
Generally, only the saw was powered, and the logs had to be loaded and moved by hand. In the Netherlands, wind power was used to winch the logs from the water into the windmill. The wind powered saw blades then cut the logs by either horizontal or vertical saws; the saws for the vertical consisted of several fixed to a frame. An early improvement was the development of a movable carriage, to move the log steadily through the saw blade.
In the 18th century the circular saw was also being used. This can be seen at work at Simonsbath saw mill in the Exmoor National Park, also at the Estate mill at Gunton Park in Norfolk where a working frame saw and early circular saw have been put back to work. The first wind powered saw mill in the UK was built in 1657. Several small estate corn mills also had a saw bench powered by the waterwheel for converting estate timber for building purposes.
Details
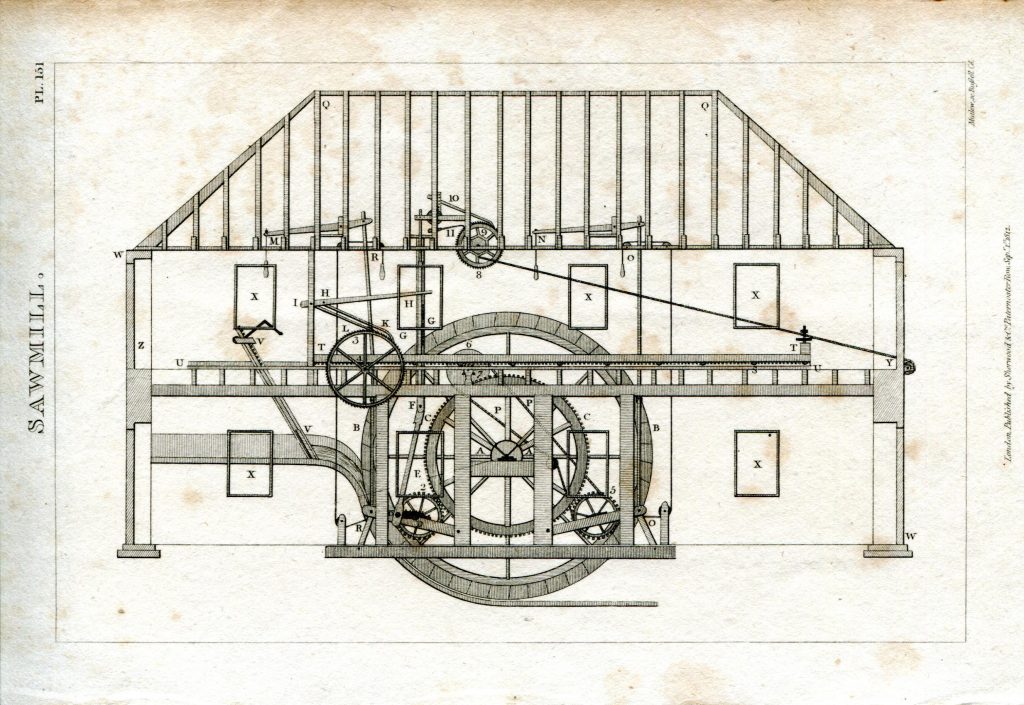
Saw mills, both wind and water powered can still be seen, some working examples and some in museums. Their purpose was to saw trees into planks for building material and other useful wooden objects.
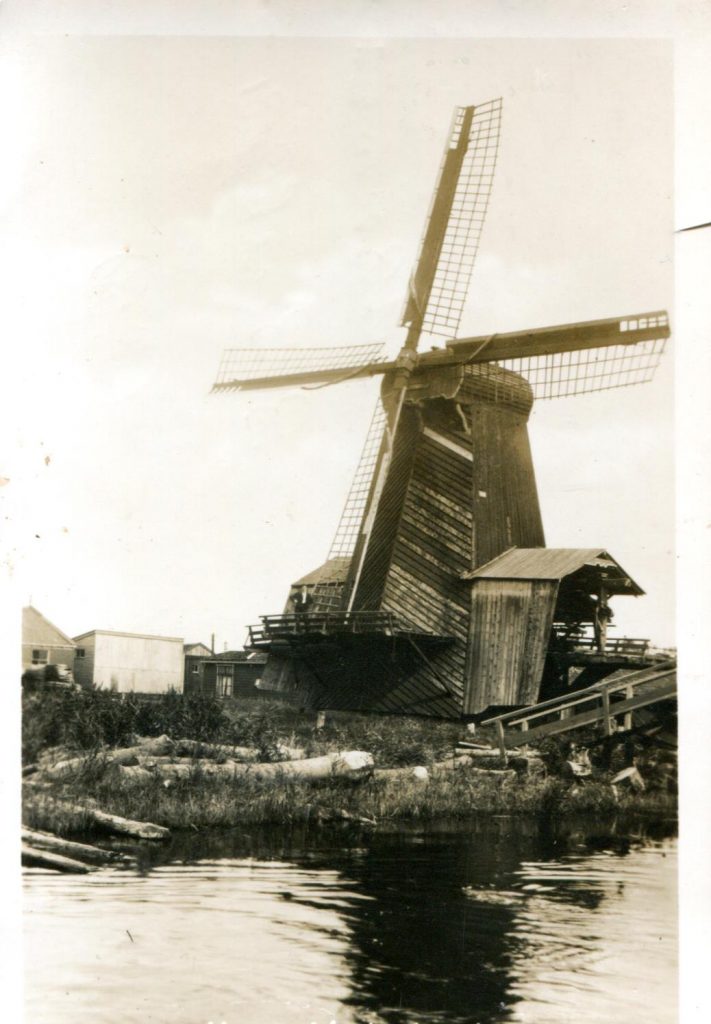
Saw mills can be found in most countries around the world. The Netherlands is particularly renowned for its wind powered saw mills, many used in shipbuilding and many still working today. In the UK the first wind powered saw mill appears to have been built in Lambeth in 1657; it was a smock mill constructed on Dutch designs. Others followed throughout the country as the trees were cut down in woodlands and forests to make way for housing the growing population. The saw mill could convert the timber into building materials for timber framework, floorboards etc.
The wood used would depend on what was available – for example, Oak, Apple, Hornbeam could be sawn to make blank cog wheels for a mill. The trees once cut down would have to be submerged in water for several months before being sawn – this helps them to stop splitting and warping. The timber was then hauled into the mill and then onto a frame where it was secured.
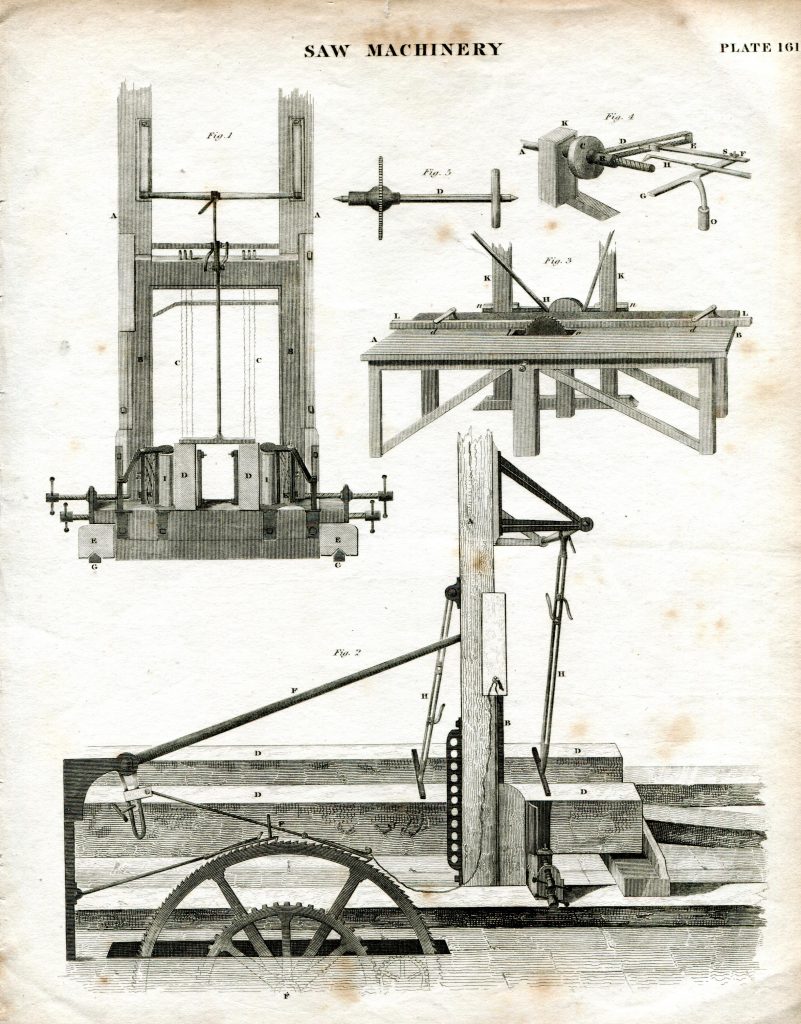
There are two types of saw mills, the vertical and the horizontal, depending on which way the saw blades operate. The saw frame consists of several saws, each being 9 or 10ft long, and move up and down as they saw through the timber. The saws in the mills could be adjusted to cut any desired thickness. Gearing allowed various functions which included getting the timber into the mill to the actual sawing itself. Spare saws would be kept in the mill for replacement while others were being sharpened or needed changing over for work on different types of hardness of woods. On average, saws would be taken down and sharpened around every 50 meters of wood cut.
Wind driven saw mills are of course dependent on the wind, and some today have electric motors to use in case of a calm period, but if the wind increases too much then the mill has to be stopped to furl the sails. In the UK only one wind powered saw mill now survives, at Buckland in Surrey. It is believed to have been built around 1860, but seems to have only worked for a short time a steam engine was introduced. Today it has been repaired. The saw and lathes were worked from belts driven from a line shaft directly from the windmill sails. There were once around 20 or more small saw mills like this existing.
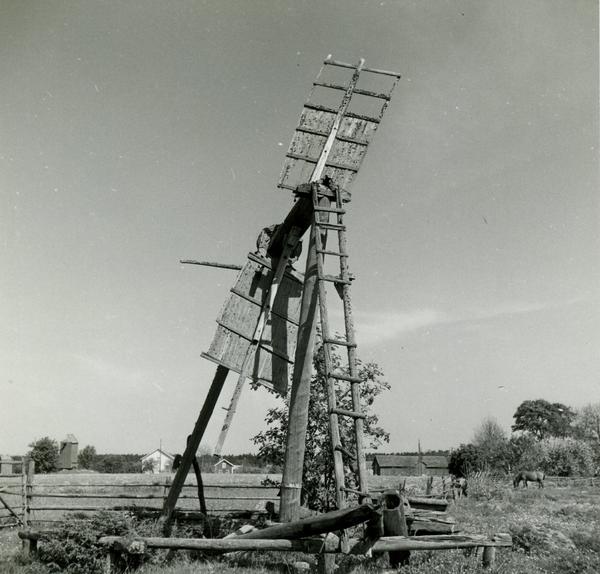
In the UK water powered saw mills were usually built where water was easily available and many were on country estates. This would help the owner with repairs to his properties and also for firewood. Some were purpose built and others were attached to a watermill producing flour. On Mapledurham Estate in Oxfordshire a saw bench was built outside the watermill driven by the waterwheel, this was for sawing wood for the Estate. (see image) Another one still surviving is on the Ingleborough Estate in Clapham in the Yorkshire Dales, driven by a turbine.
Some other surviving saw mills are at Gunton Park in Norfolk; Gayle Mill in Wensleydale; Simonsbath situated on the Exmoor National Park; Dunham Massey, Cheshire; Combe Mill Oxon; Kirkdale Estate in South West Scotland; and Pontdolgoch in Wales. The Bobbin mill at Stott Park produced bobbins on lathes and saws for the cotton mills. The bobbins were made from coppice wood of alder ash, birch and willow.
Personal experience of running a wind powered saw mill in the Netherlands.
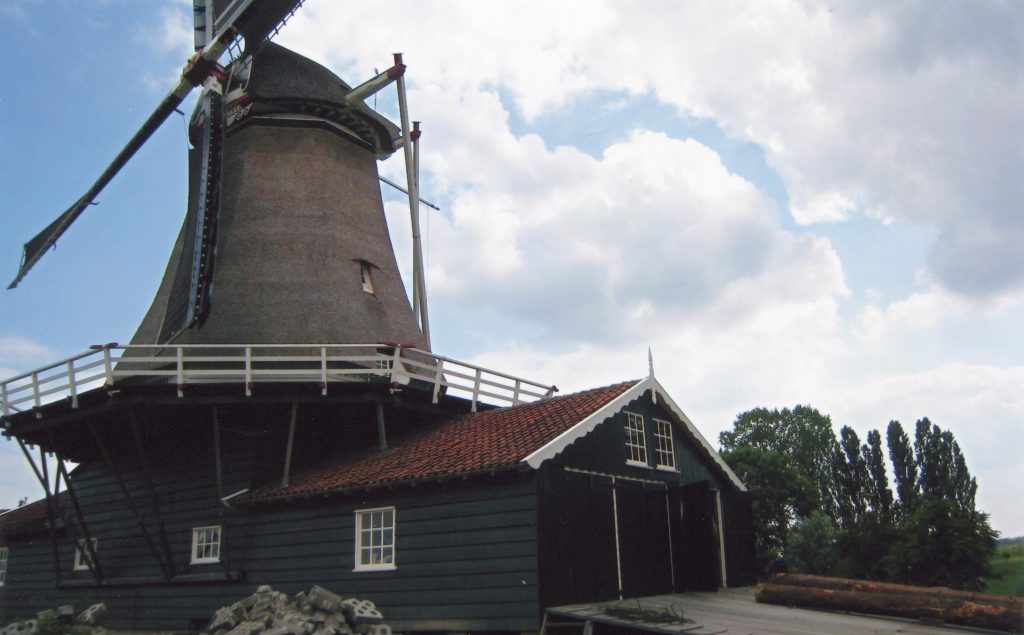
The mill I helped operate was the Bolwerksmolen sawmill, Deventer. It is on the west bank of the river Ijssel, near the Wilhelmina Bridge. It was built in 1863 and is an octagonal thatched smock mill standing on a square barn with the slipway which allowed the logs to be pulled out of the water into the mill.
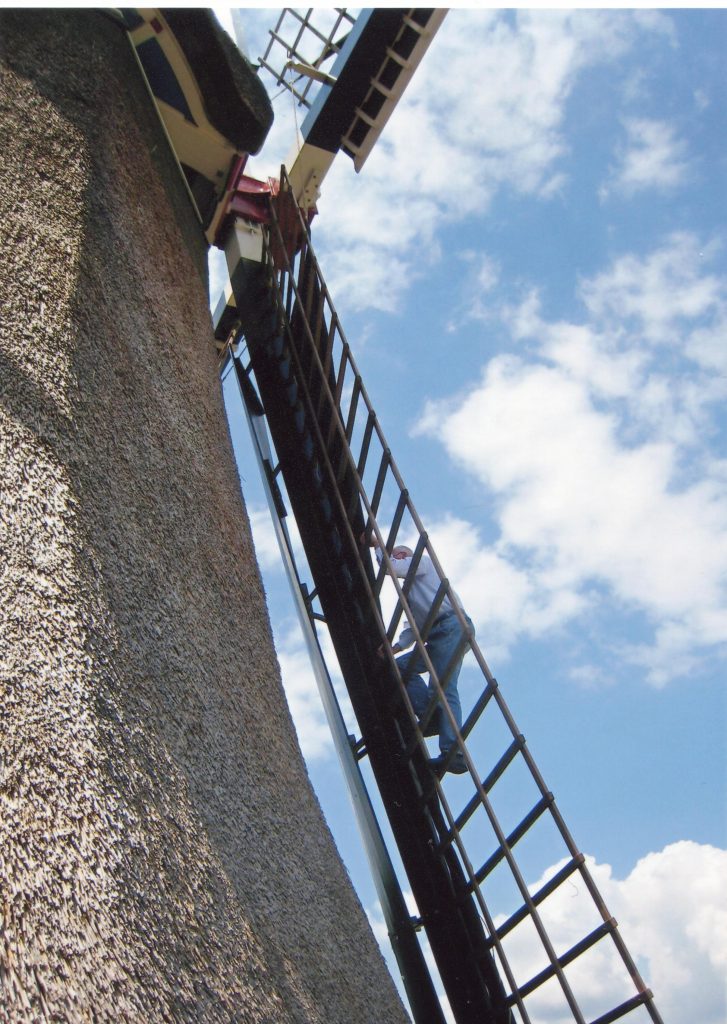
I was privileged to help run the mill on a TIMS symposium visit. At first I was rather disappointed as I put my name down to help at an oil mill (for linseed oil) with edge runners turned by donkeys. But after arriving at the windmill I was happy to get involved. The first job was to set the sail clothes on the windmill sails, then the job of hauling the baulks of timber out of the water next to the mill. This was first achieved by using a long pole with a rather vicious hook on the end to secure the tree trunk which had been in the water for many months.
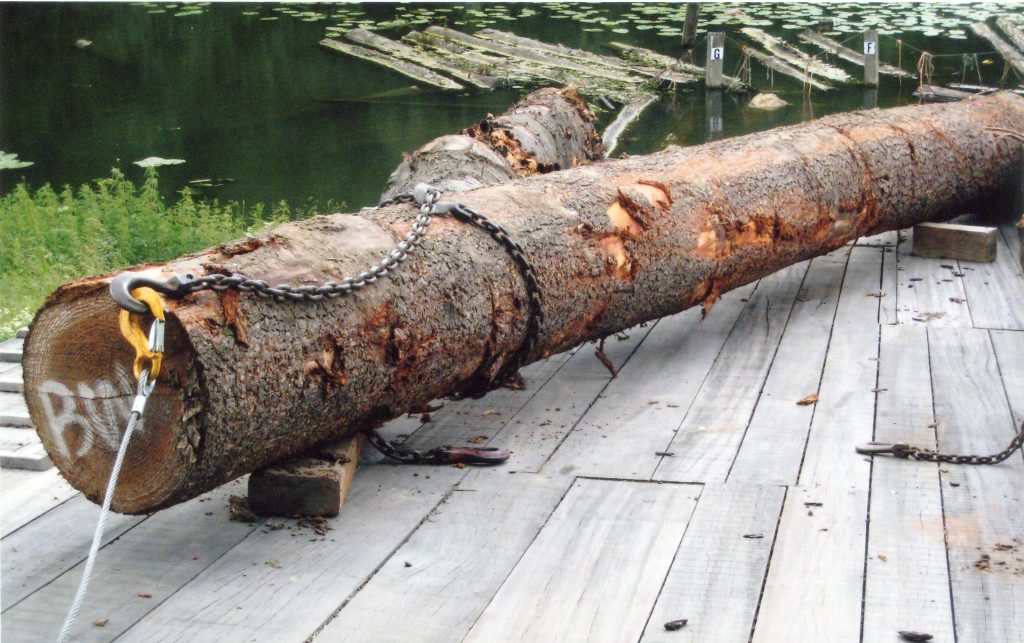
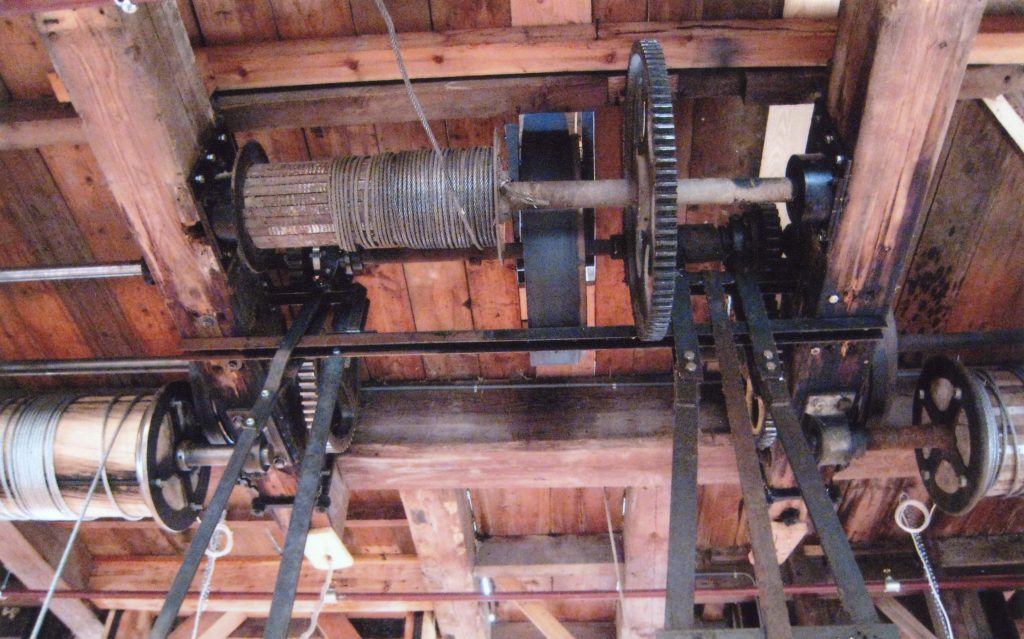
At this mill the logs were brought as rafts to the mill by water, but at another mill I visited the logs were kept in the water by the mill and I had to walk over several in the water to help choose the right ones. They floated quite happily thank goodness although it was a little nervous taking the first step.
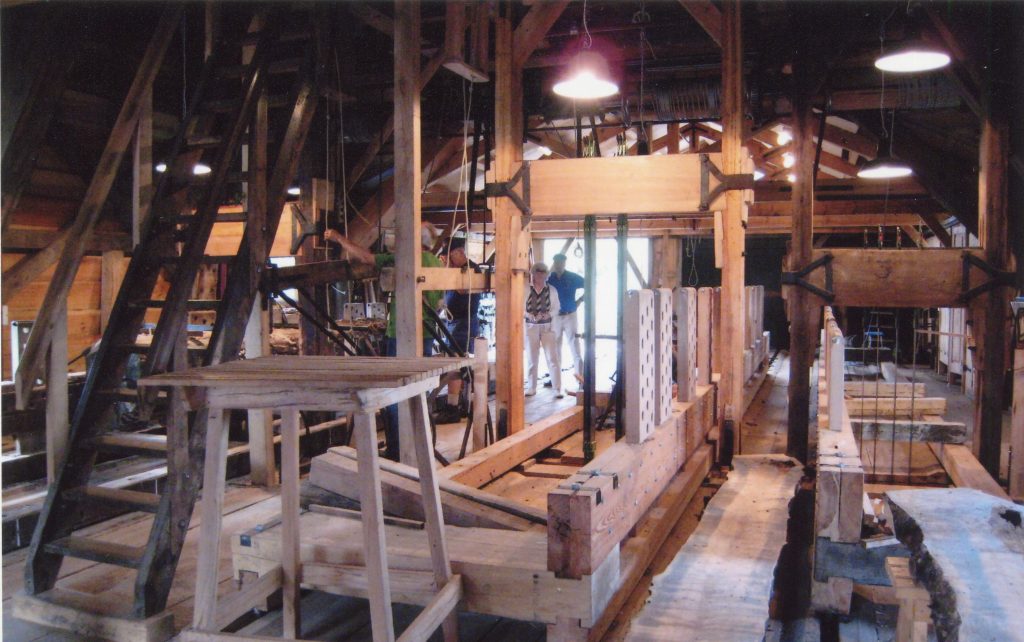
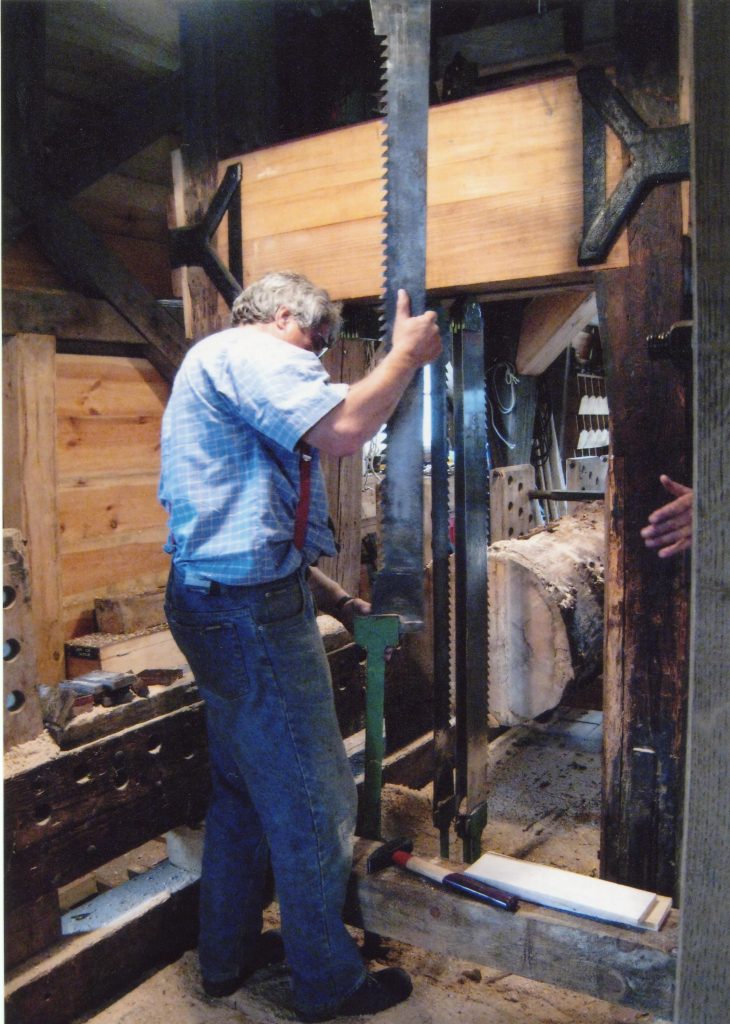
Once the timber was near the landing stage, it was attached to a chain and using the power of the windmill sails, dragged into the mill for sawing. The mill had three saw frames each with multiple blades. A log was turned into planks in one pass through the saw. Many spare saws were hung in the mill as they often needed taken down for sharpening. Each time a blade was changed over it took around 45 minutes. Once a log had been cut the planks were stacked outside in an open sided shed.
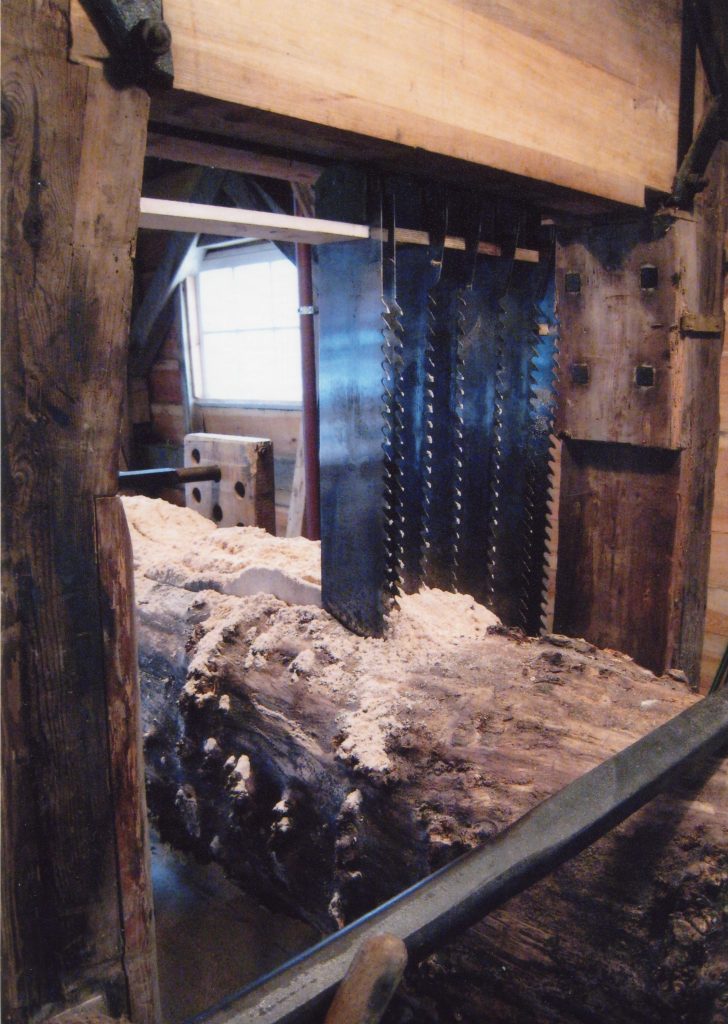
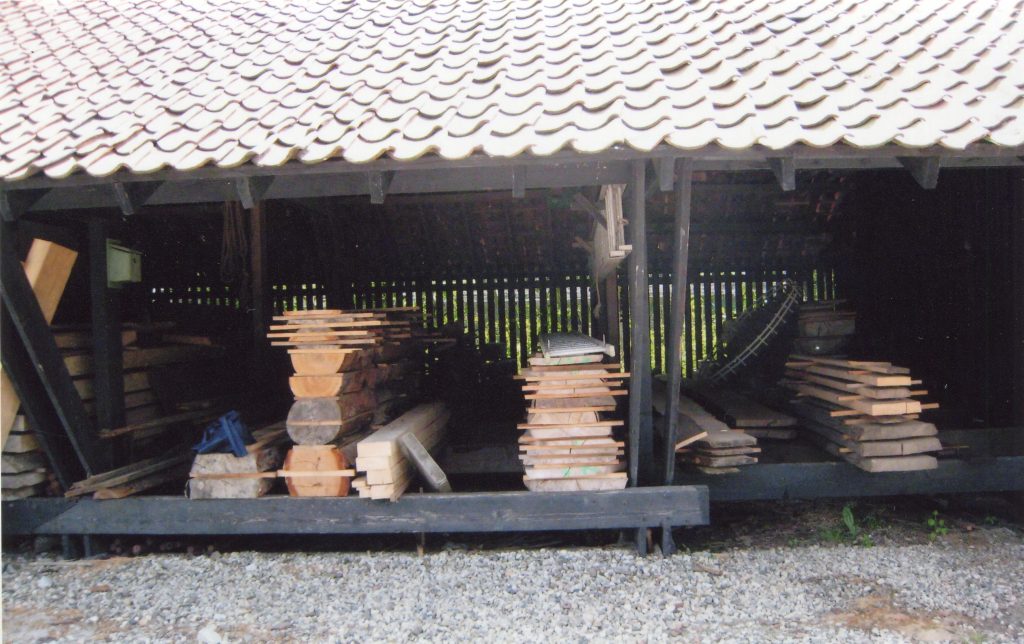
Links
Images and documents in the archive catalogue
Saw mills in our database:
From elsewhere on the web: