Though the use of iron in millwrighting is not as traditional as that of wood, iron has firmly cemented its place as a valuable material in the craft. Two types of iron have been used in millwrighting, these being wrought iron and cast iron. Wrought iron was used mainly for bearings and hinges, as it was iron that you needed to heat up and then manipulate; its properties are also suited to areas where strength is needed. Cast iron, on the other hand, became increasingly popular in millwrighting after being pioneered by John Smeaton in the mid-18th century. This is likely due to its convenience, as you only had to melt the iron and pour it into a mould rather than manipulate it. It also had many benefits, such as a long lifespan. The use of cast iron has therefore grown exponentially in millwrighting over the past few centuries. | |
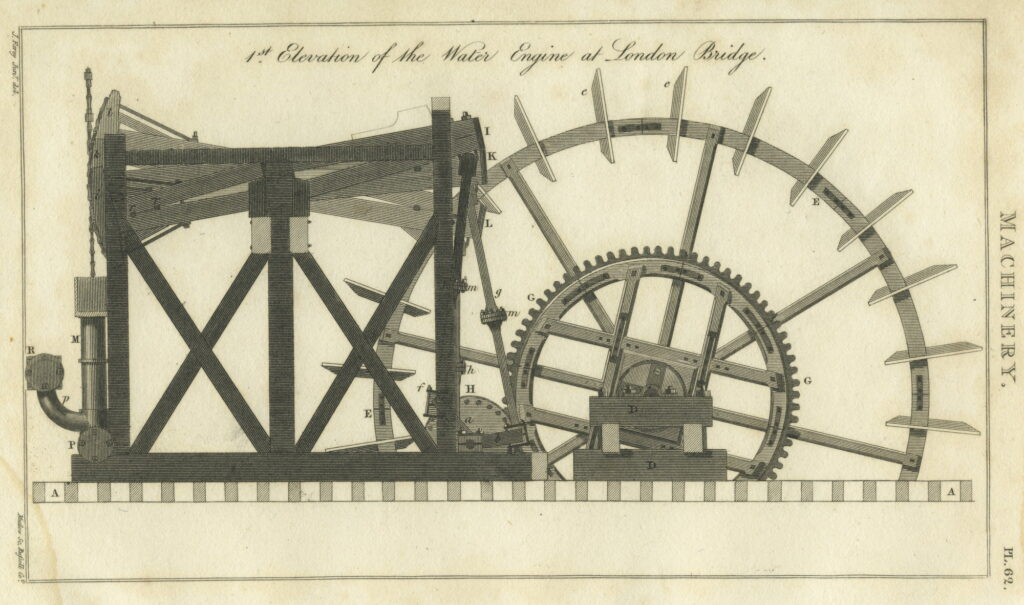
(Mills Archive Collection, JKMC-1121641)
Cast iron began to be increasingly introduced into millwork in the mid-eighteenth century. In comparison to wood, there were advantages to using iron in the construction of certain parts of the mill, especially in watermills. Iron could be used for parts of the waterwheel that were consistently submerged, and unlike wood, it would not be susceptible to rot. To begin with, iron was reserved for hubs and rims of the many composite wheels that were installed, as large castings presented many difficulties. At the latter end of the eighteenth century, owed mostly to the work of John Smeaton, the ability to cast iron was improved and many fine wheels were produced. After this innovation, timber was, in most cases, retained only for the floats and paddles of a waterwheel. The pit wheel was also gradually crafted from cast iron. It could often be partly submerged, and in such conditions the superiority of iron was indisputable. However, the teeth of the pitwheel would likely remain wooden as they were easier and cheaper to replace if they broke. The miller would likely have spare wooden teeth ready to replace those that broke to keep the mill working. It was also typical to cast the wallower in iron once the ability to do so was available. The iron wallower meshed nicely with the wooden teeth of the pitwheel, and it was common for iron and hardwood to work in tandem as they worked quietly together. Iron construction was slowly adopted for the remaining machinery of the watermill, though timber was still employed for the main waterwheel shaft which transmitted power through the wheel. In some cases, millwrights would replace this shaft with an iron one as it could last a lifetime, rather than 35-50 years. In multiple surviving cases, the great spur wheel is also made of timber. | |
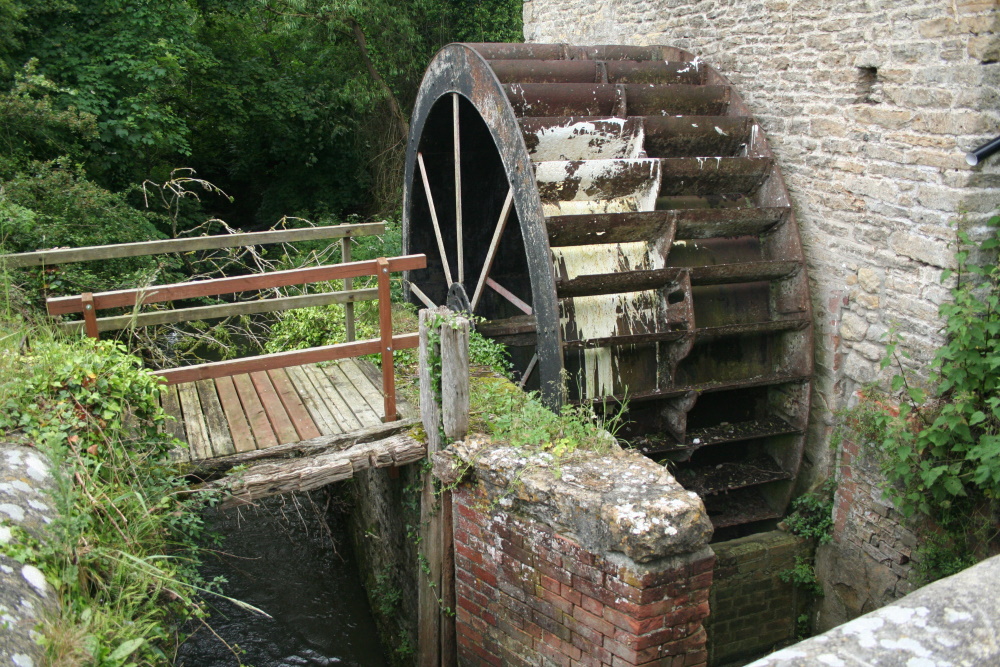
(Mills Archive Collection, MBRN-DOP-088)
Iron also had importance in the construction of a windmill, though its usage was far less common than in a watermill. Most parts of a traditional windmill were constructed of wood, however, in some parts of the mill, such as the mortises where the stocks passed through the windshaft, the usage of timber presented a weakness. This area was particularly susceptible to penetration of rainwater and therefore more likely to rot. The introduction of cast iron aided in ending this problem as the end of the shaft was replaced with an iron casting, known as a poll end or ‘canister’, and the stocks were secured by wedges. The wooden gearing that existed in a windmill took a similar route to that of a watermill. Composite brake wheels were introduced into the windmill as the use of cast iron steadily increased in the late eighteenth century. Some windmills also had brake wheels completely made from cast iron, though wooden gearing never fully gave way to metal. Wooden wind shafts were also replaced with a cast iron version as they offered the advantage of not wearing down due to friction at the neck. Also, if a mill wanted to change from common sails to patent sails, it would need to have an iron windshaft as the millwright would need to drill down into the middle of it. Therefore, during the twentieth century, iron wind shafts were incorporated into new work wherever possible. Iron also featured in the advancement of roller mills. During the development of roller milling, Britain began to prefer iron and steel in its production of roller mills as they only needed regrinding once a year. By the late 1870s, chilled iron roller mills began to be installed across Britain, and this provided a more efficient way of grinding grain to produce flour. |
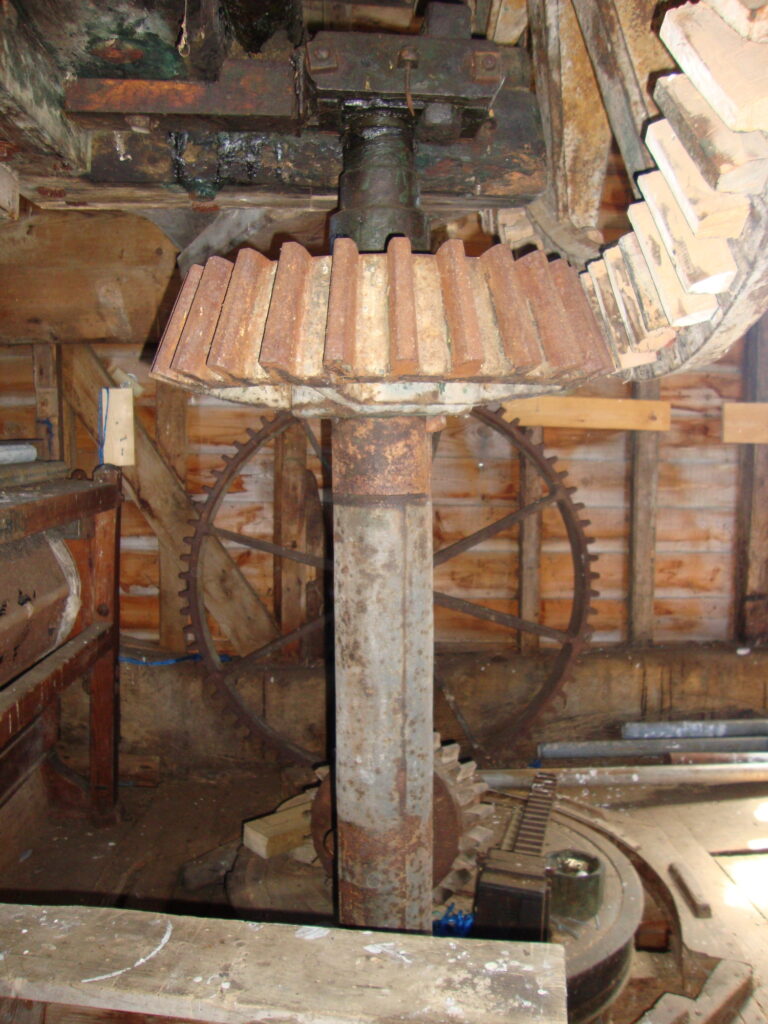
Photo Guy Blythman
(Mills Archive Collection, TECH-FRIS83)
In all, iron has been, and still is, an important material in the craft of millwrighting. Though the traditional craft of millwrighting never fully moved away from its roots in wood, iron offered a clear solution to some issues that arose with the use of wood. |