Since mills first appeared in Britain, the main material that has been used to construct them has been wood. The first mills reported in Britain date back as early as the Domesday Book in 1086. Though there is no mention of windmills, it is confirmed that both water and animal powered mills existed at this time. The first authentic record of a windmill is dated slightly later in 1185, when a windmill in Weedley, Yorkshire, was let for the price of 8s. per year. Following this, the first illustration of a post mill was featured in the English Windmill Psalter published in 1260. Though some of these mills may have used stone or brick in their construction, most of them would have either been built out of wood or had wooden machinery on the inside. |
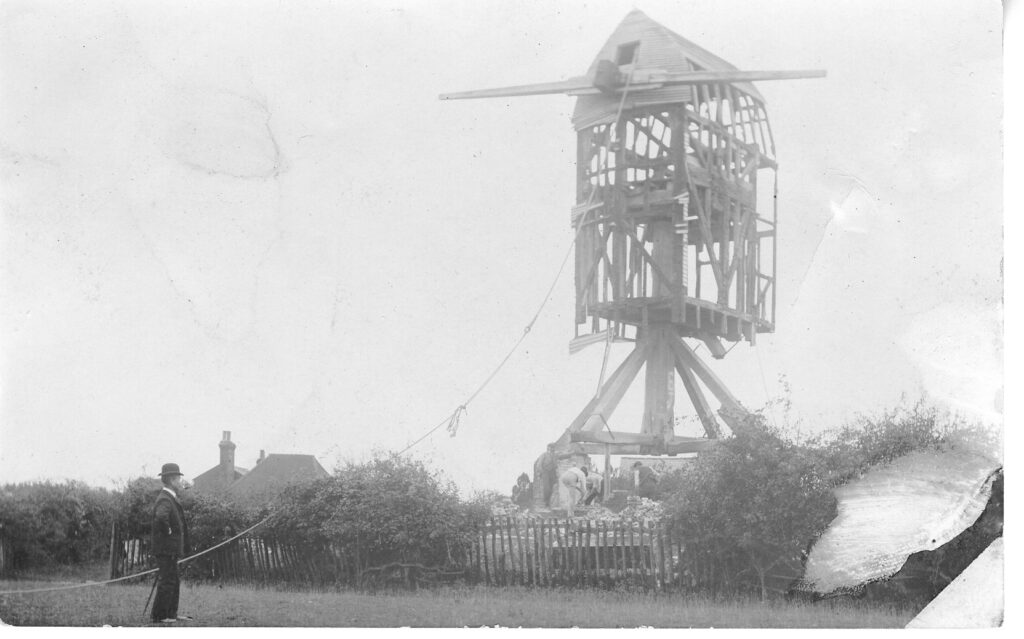
https://catalogue.millsarchive.org/post-mill-in-course-of-demolition-2
The choice of wood to build a mill from required a careful selection process, especially for the mill’s main features. Wood was seen as a good material to use due to its durability and availability. It was generally accepted in the past that oak, which was barked in the springtime and felled in October, provided the toughest all-round material. Mills have therefore tended to use oak in their construction where available. According to Stanley Freese, the oak used in the crafting of a mill should be felled when it was about 100 years old to the correct strength and maturity for making a mill and its components. If the oak was felled between the age of 50-70 years old it was not mature or hard enough, and if felled around 150 years old it is likely the wood would get brittle. The main post and the crown trees of a post mill tended to be made of oak, though Freese noted that the crown trees may be constructed out of pitch-pine or ash if needs must. However, if they were not made of oak they should be quartered and reversed to maintain the strength needed to support the mill. The timbers of the main body could have been made of oak, or if good quality oak was unavailable, pitch-pine or sweet chestnut could be an alternative. The stocks had been previously made of English oak when it was plentiful, however pitch-pine stocks were later used as a substitute. The arms of the sail were preferably made out of pitch pine, which was likely due to the durability of the wood. The gears, such as the brake wheel and the wallower, were wooden to begin with, though in more recent times the wallower has also been made of iron. Older brake wheels were made of oak or another similar durable wood and the cogs were often made of apple wood. Surrounding the brake wheel there was a brake which is made up of wooden ‘shoes’. These wooden shoes would usually be made of ash, elm or poplar, likely because of their resistance and the fact that they were susceptible to steam bending. |
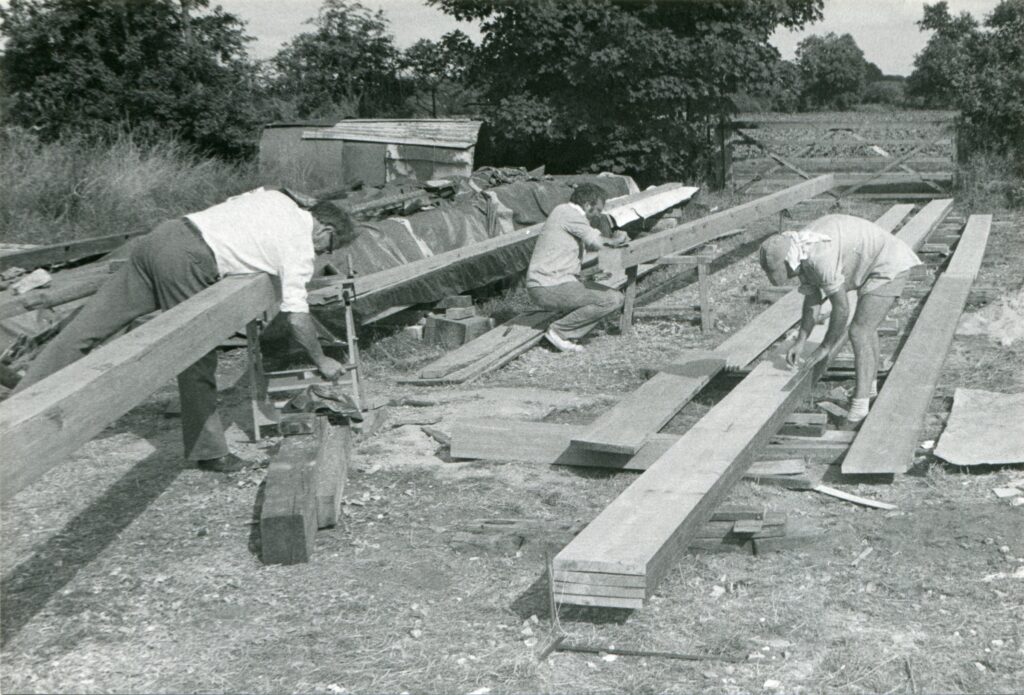
https://catalogue.millsarchive.org/stocks-and-sail-whips-tower-mill-thelnetham
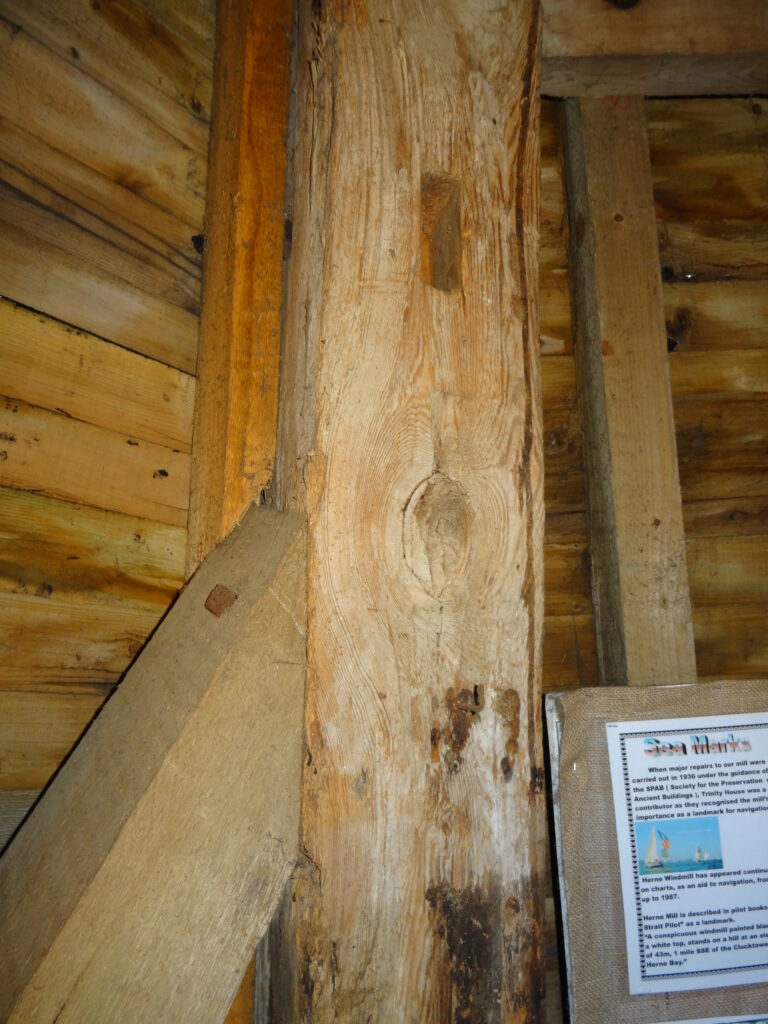
Smock mills used wood in their structure, with their cant-posts made from oak or pitch-pine that met at the angles of the mill. The outside of the mill was also weatherboarded with timber to protect the wooden structure and machinery. The cap of a smock mill, which turned the sails to the wind, would also have been crafted out of wood. It sat on a curb, a set of runners, which allowed the cap to turn.
Cant post of the Smock Mill in Herne, Kent
https://catalogue.millsarchive.org/cant-post-smock-mill-herne
Early versions of the curb were made out of wood but later cast iron was used. Wood also featured in the construction of watermills. The building that contained a watermill had to be a secure, well-built structure. Because of this, wood, stone or brick was used in their construction depending on their location. Wooden cogs featured in the gearing of a watermill. This was down to the fact that they were easier and cheaper to replace than their metal counterparts. The wood used, in this instance, would depend on the gearing’s location in the mill and how quickly it was turning. |
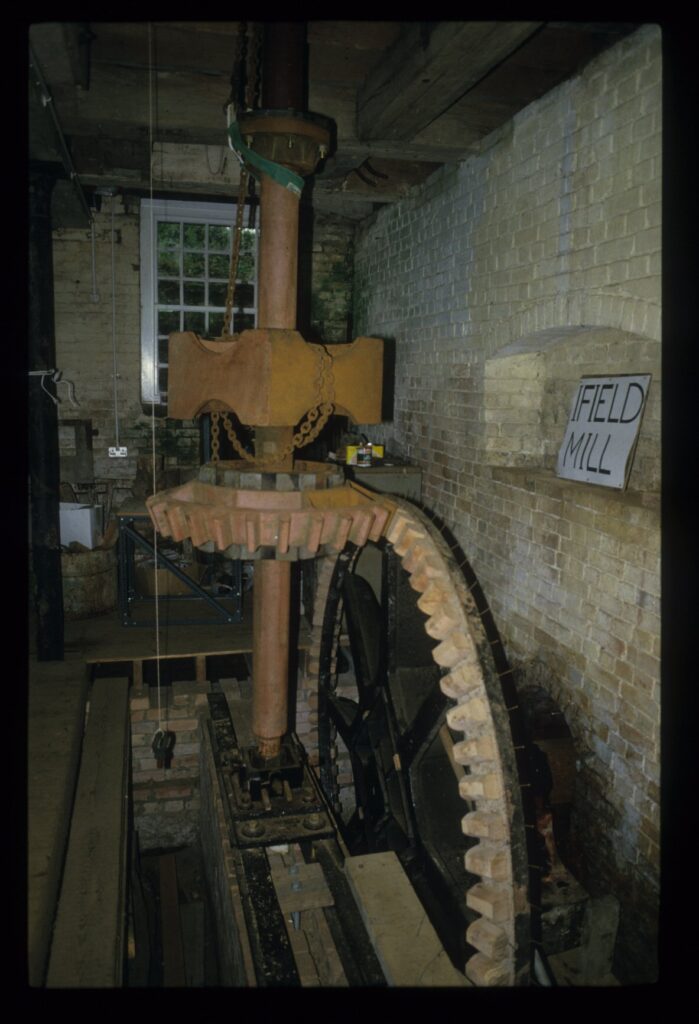
The teeth of the pitwheel would have been crafted from oak. The pitwheel would turn at a slower pace than the rest of the gearing, and therefore a wider-grained wood like oak was used. As we move up the watermill, the spur wheel could have been made from wood or be cast with an oak rim. The crown wheel may also be wood, or cast in iron with a wooden rim, and it would have wooden teeth.
Interior of Ifield Mill, Crawley, 1985
This shows a pit wheel with wooden teeth working with an iron wallower – this displays how wooden and iron parts of the mill could work in tangent https://catalogue.millsarchive.org/interior-ifield-mill-crawley
Both the spur wheel and the crown wheel would turn faster than the pitwheel so a narrower grained wood would be used for the teeth, such as beach or applewood. Some parts of a watermill would have continued to contain wooden cogs in its gearing even as cast iron became more available. Most waterwheels were constructed entirely of wood to begin with, with the rim crafted of oak and the paddles of elm. They were produced in two different styles. One style was the compass arm which was known to have a weak axle due to the way it was constructed. The other, and the more favoured style by the millwright, was the clasp arm. On this wheel the arms crossed from rim to rim, two pairs on each side, each pair clasping or fitting tight up to the sides of the axle tree. Later on, the construction of waterwheels featured both wood and cast iron, this was likely to reduce costs for the miller whilst offering them a more balanced wheel. |
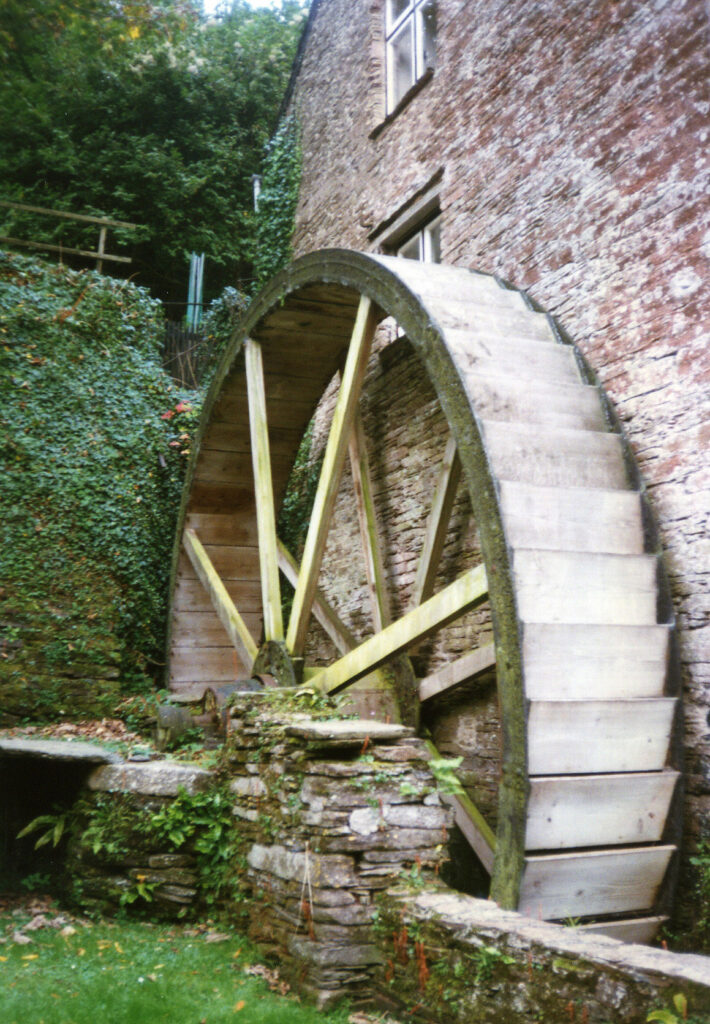
https://catalogue.millsarchive.org/deerbridge-waterwheel
In all, wood was, and still is, significantly important for the making of mills and millwrighting. Traditional windmills heavily feature wood as part as their structure, gearing and sails. This piece offers a very brief and untechnical overview of the use of wood in millwrighting and the construction of mills. I have attempted to offer an insight into the features that would have been constructed using wood and which wood was likely used if known. Though the type of woods vary from mill to mill, the standard wood of choice in England tended to be English oak. If this wasn’t available then pitch-pine was considered the main alternative. Other wood suited different needs, such as ash or poplar for the brake shoes. Features of the watermill, such as the hurst frame, were traditionally crafted out of wood, and the gearing, such as the pit wheel and spur wheel, also featured wood. Waterwheels were constructed of wood until the ability to make cast iron parts or wheels was developed, even then a mix of both iron and wood could be used. Wooden cogs were also used in watermills, and likely in other mills too, due to the fact they were easier and cheaper to replace than those made of metal. |