Last May I featured William Gardner of Gloucester in a brief review of 10 succesful milling engineers with works in the UK. |
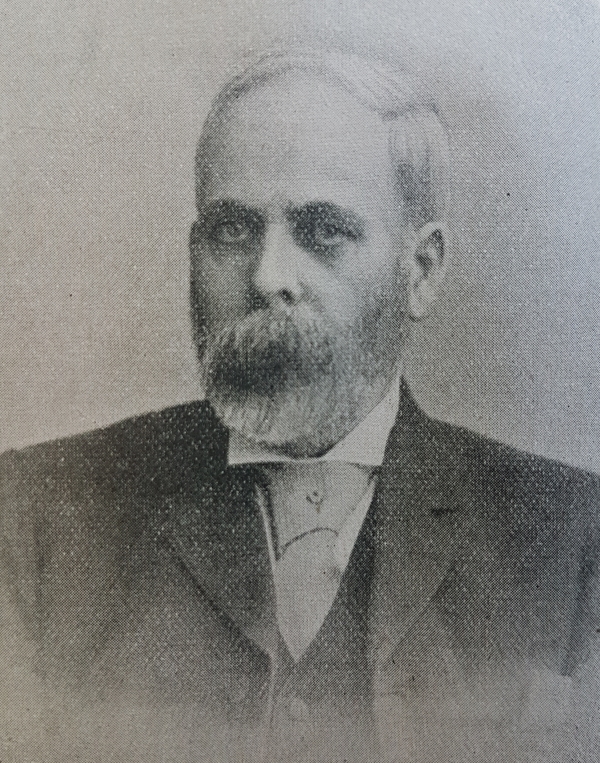
In The Miller (5 August 1895) there is a detailed account of this highly regarded firm, well-known in Gloucester and the West of England since the 1870s. The firm underwent several moves since it was founded around 1860, culminating in new premises in Bristol Road, completed when plant was installed in June 1894. Once established there Mr. Gardner took into partnership his sons, Charles and Alfred, styling the firm as William Gardner and Sons.
William Gardner, millwright
The ground floor offices accommodated a little room in which a telephone was installed so Mr. Gardner could take a call immediately from a client “in any part of the kingdom” as well as a strong room with an iron door for holding valuable papers which “would withstand a charge of dynamite”! Charles Gardner, as general manager of the works could see, through a glass window, the whole length of the fitting and turning shop which ran longitudinally to the offices. |
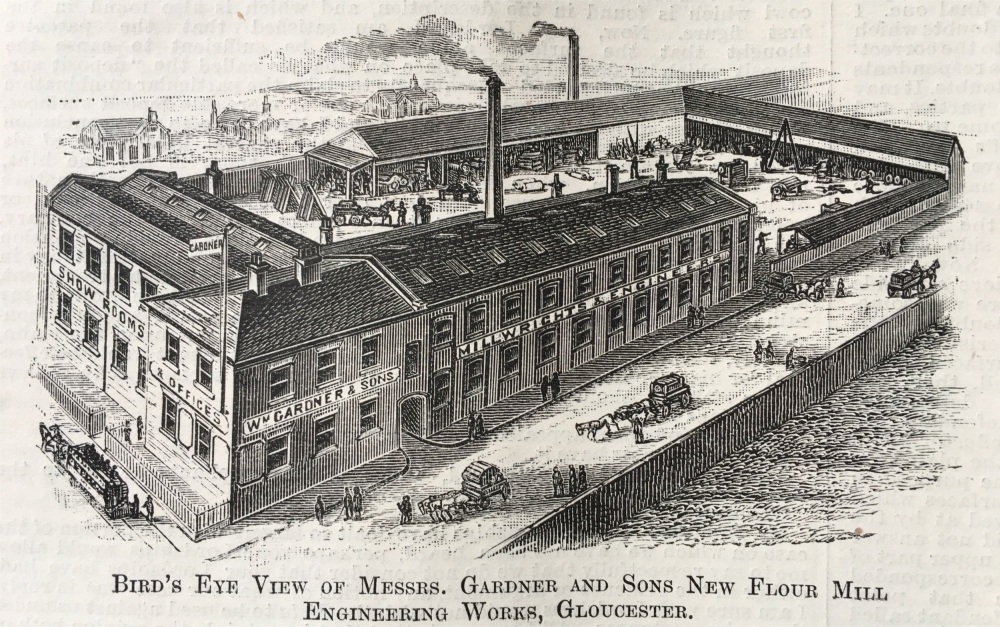
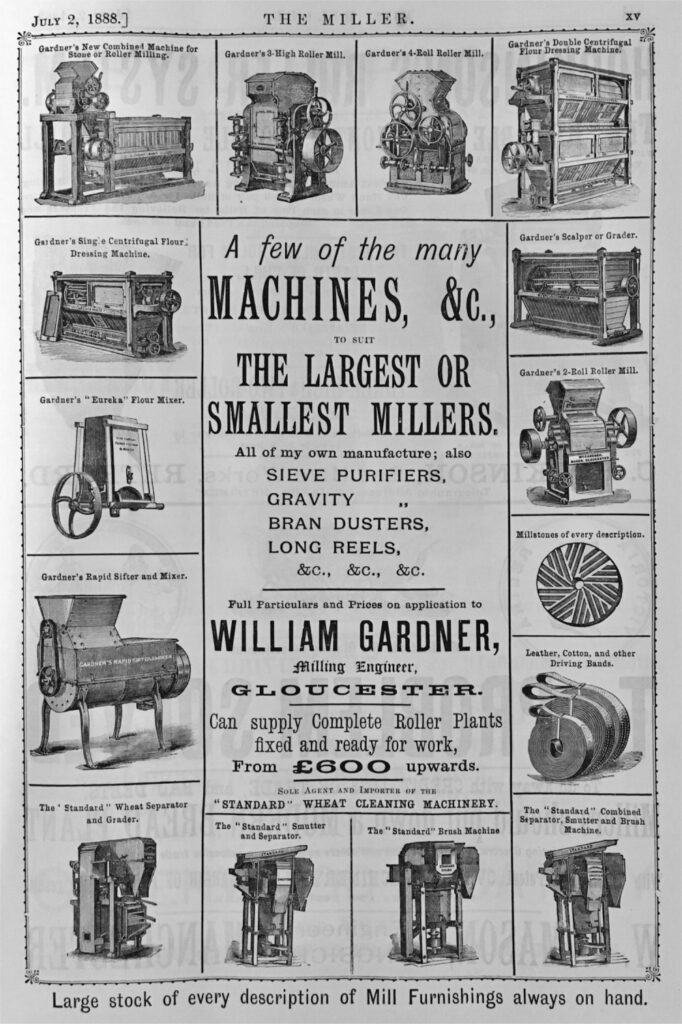
The fitting shop was supported on two rows of iron columns carrying a line of shafting and held all kinds of machines being made ready for work. Roller mills were evident in all stages of completion as well as centrifugals and ordinary reels, rotary scalpers etc. There was a fine lathe capable of turning 20 feet of shafting and of boring out large wheels. An overhead crane served the whole length of the shop.
Gardner devoted much time and attention to the grinding and grooving of their rollers in a separate department furnished with the latest design of grinding and grooving machines. Rolls were sent from all parts of England and Ireland to be grooved, where any spiral or shape, or number of corrugations could be readily matched.
1888 Advertisement emphasising Gardner’s work for mills of all sizes
Outside the fitting shop a large yard held a shed containing a wide selection of iron bars and in another, planks of raw wood were dried. Particular attention was paid to the enormous stocks of cog gearing timbers such as hornbeam, crab tree. Another shed contained pulleys, hangers, power possers and worms etc. The millstone department stood by itself. One shed contained a line of hurstings, another a collection of rough stones ready for millstone building, with the finished stones stored separately. |
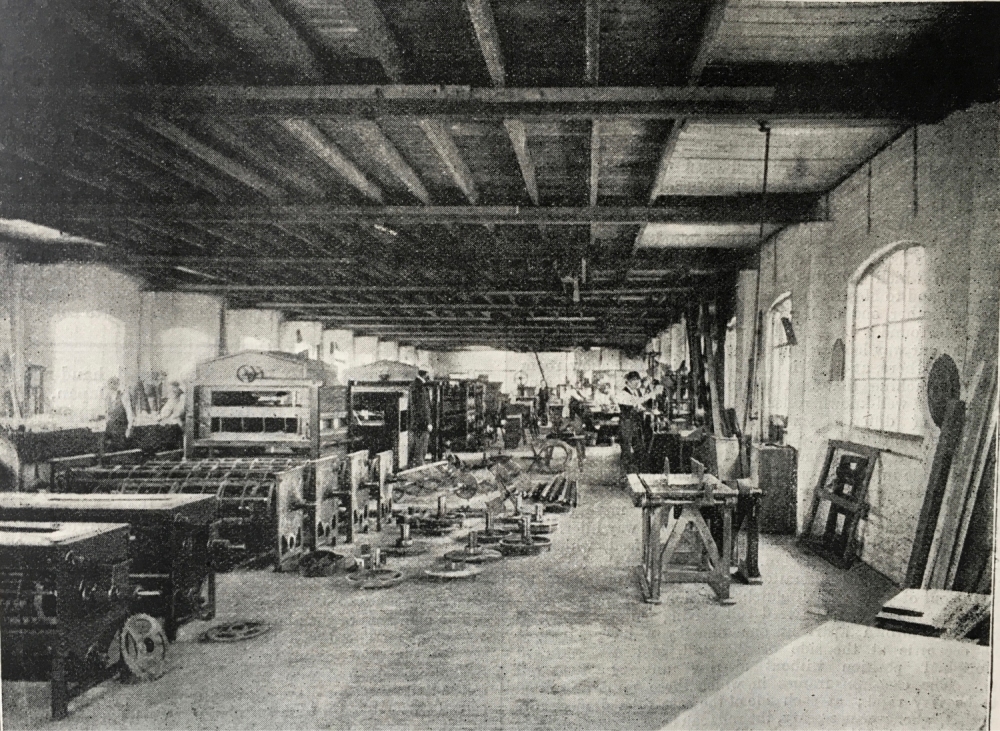
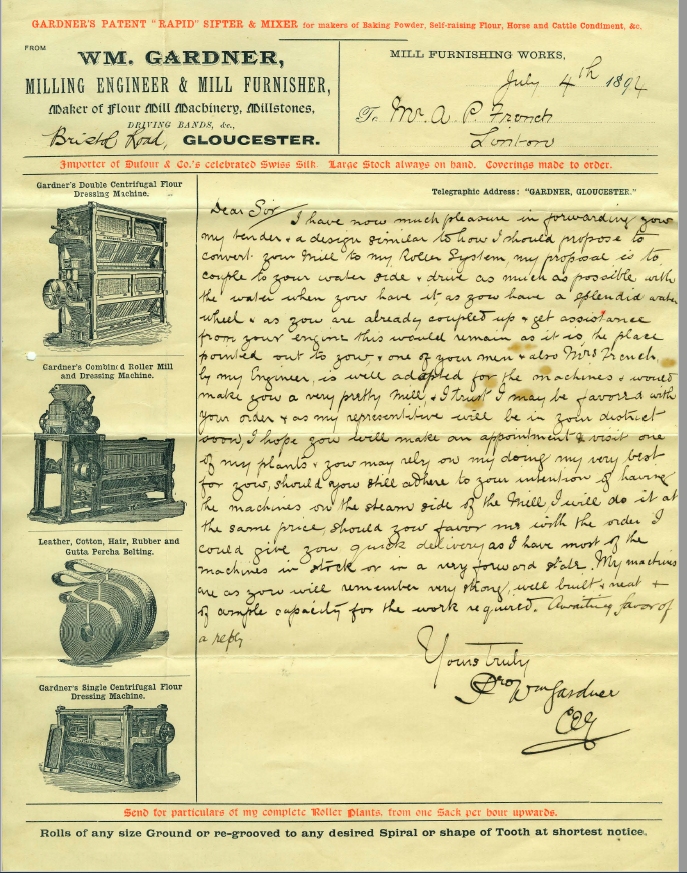
Although the millstone had seen its day in flour milling, there were yet many industries in which grinding stones of different patterns and diameters were used and Gardner did a fair trade in these. The firm’s work with smaller mills featured in their advertising and is nicely illustrated with a tender from July 1894 in one of the Mills Archive collections offering the miller new equipment that would “make you a very pretty mill”.
Covering letter for tender by W Gardner to install a roller mill system
The upper floor held a fine showroom filled with finished machines ready to leave the works. |
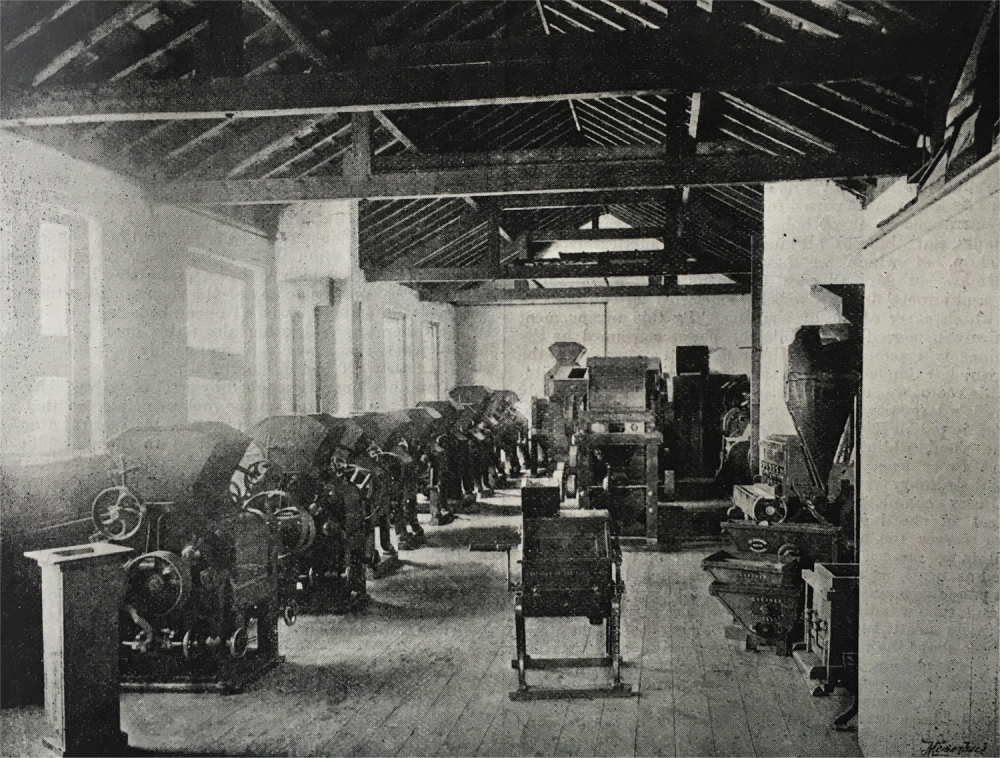
A line of Gardner’s roller mills made an excellent impression. These mills were of different sizes, fitted with rollers of different diameters, varying between six, seven and nine inches. There was also a sensitive automatic feed that could be cut off without any alteration of the feed adjustments, by merely throwing out of gear a small clutch, the handle of which was conveniently placed by the side of the feed roll driving pulley. The two pairs of rolls would be thrown apart at one time by a lever attached to a double eccentric at the side of the mill, and returned to their original position without altering any of the roll adjustments. The cast iron frames in which the mills were fitted were very rigid, and at each side of the case filleted pieces were arranged so that whenever necessary, the rolls could be easily and quickly changed, without removing the hopper. All the adjustments were outside the frame; the arrangement rendering it easier to take the mill to pieces whenever that operation appeared advisable. There was a special room used as a store for Gardner’s patent “Rapid” sifters and mixers, containing all sizes from a small seven pound machine to a half ton mixer.The upper floor held a fine showroom filled with finished machines ready to leave the works. |
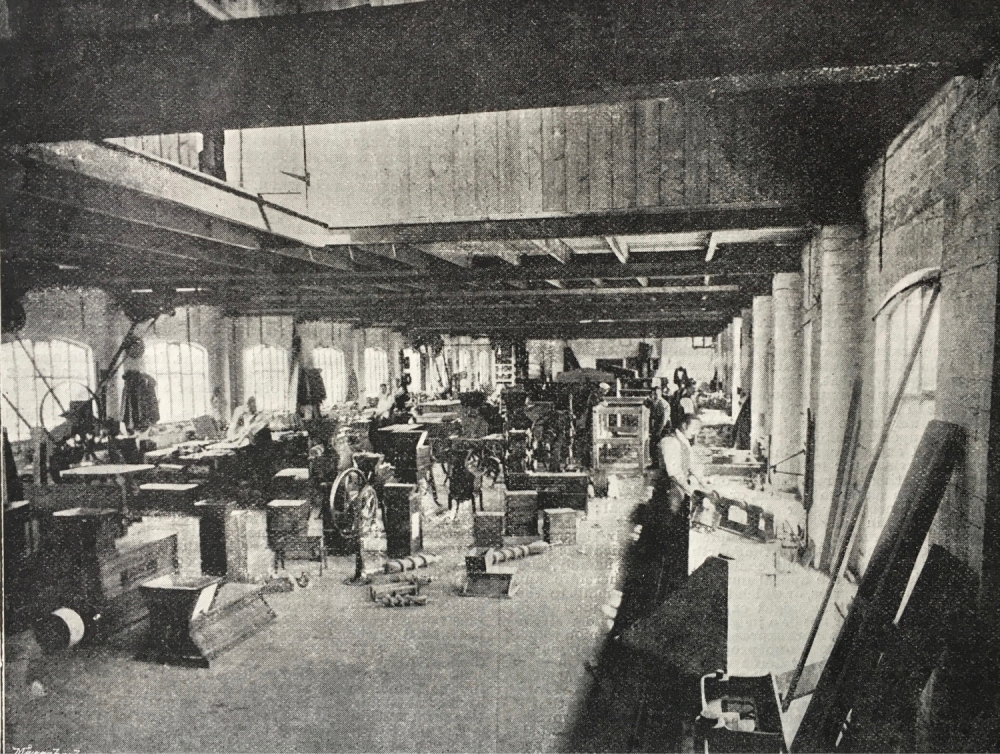
The hoppers were not constructed from thin strips of wood as many other machines were, but of a single piece of wood. A machine in the testing area was being shown as singularly effective in dealing with canary and linseed. It was fitted with a dickey sieve, and combined sieving with a reduction action for large lumps of dirt, aspirated by a powerful fan. Throughout the buildings a tramway system was used in addition to the travelling cranes, underlining the labour saving principles which the business emphasised. |